the heart and soul of blown glass
Blown glass is a vibrant material that brings the past to life and offers new emotions for contemporary design and architecture.
He plays with light and transparency, colour and texture, movement and space. It vibrates all the more because the hand of man has given it its imperfections. These imperfections keep it alive throughout the course of the sun.
It’s a material that has stood the test of time, combining tradition, expertise, innovation and modernity to delight the eye and the soul.
Ancient Glass Making
Glass has been used since prehistoric times. Natural materials such as obsidian were used. (volcanic vitreous rock) are cut by man to form arrowheads; tectites (of meteorite origin) are also used as jewellery; and finally, fulgurites are small tubes formed by the fusion of sand struck by lightning.
It wasn’t until about 2500 B.C. in the Middle East that man invented the material of glass. Craftsmen used glass paste to produce utilitarian objects containing precious, perfumed oils. These were small polychrome objects made of opaque glass. They were produced in small quantities. In this case, the technique used is that of the moulding of the glass on a core, known as the “l’core coating “, Also known as “alabastron”: a vitreous material deposited in a core of clay and sand, the shape of which it takes; after drying, the core shrinks and can be easily removed.
Later, the technique evolved and the glass mass was then poured on a table, i.e. poured and spread on a wooden table or a bed of sand.
The technique of blowing glass with a stick to make vases and other containers dates back to the first century BC in the Middle East under the Roman Empire. This is a real technological revolution. It means that glass objects can be produced in larger sizes, faster and in larger quantities. The stretching properties of the vitreous mass were exploited by eastern craftsmen, probably Syrians. The spread of this technique followed the expansion of the Roman Empire around the Mediterranean, spreading to Italy, Gaul and Spain before reaching the whole of Europe.
Paintings in the Beni Hassan Hypogeums show Theban craftsmen blowing glass with a cane in front of a fireplace, as we still do today.
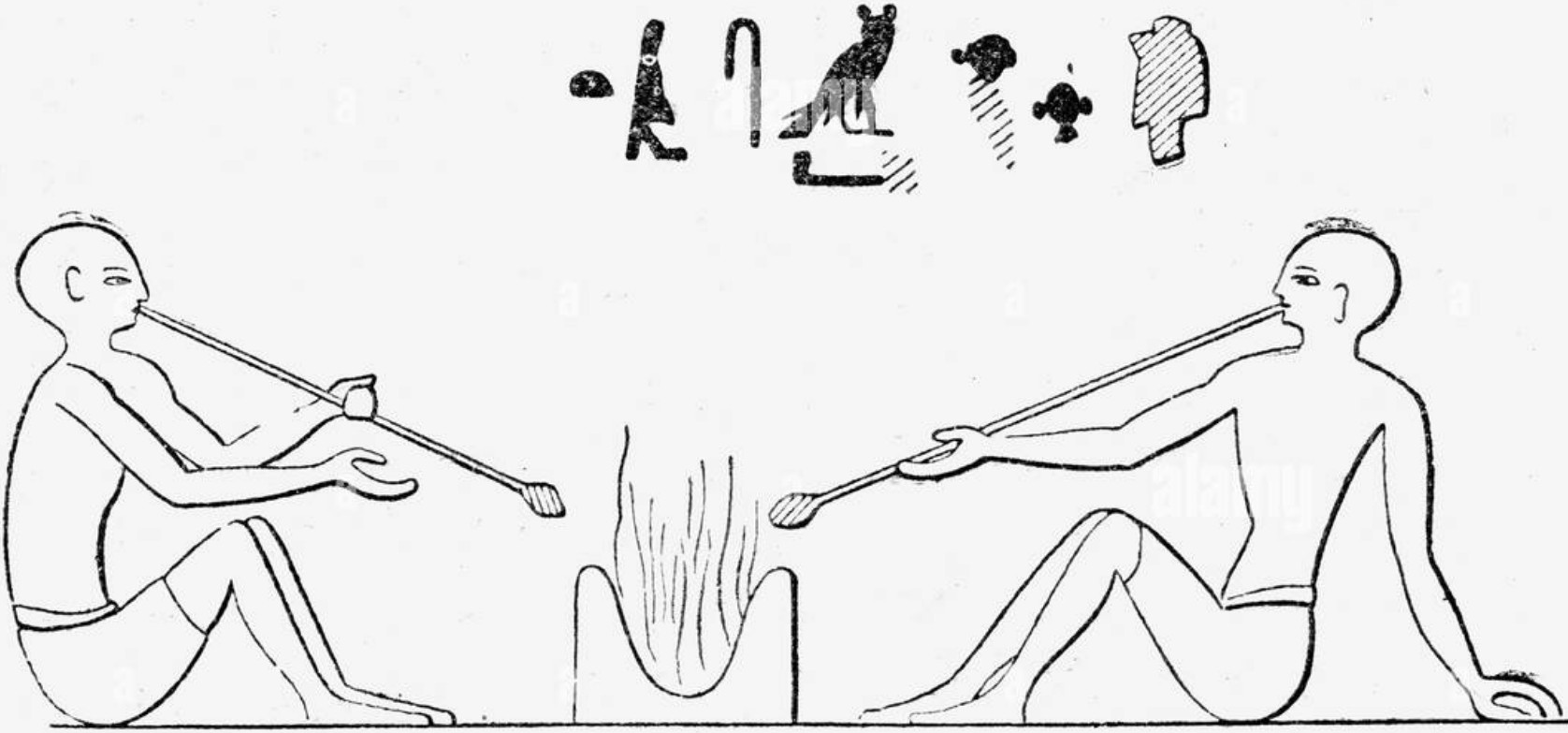
Le Verre à Vitre - Glass
Glass was first used for glazing buildings (5 to 6 mm thick flat glass for glazing windows, date back to Roman times in the 1st century AD. Remains have been found at the site of Pompeii. However, the use of flat glass remained extremely limited, even in the Middle Ages. In the past, thin sheets of mica or alabaster were the material of choice.
Window glass was known to the Romans. However, it was not widely used in civil architecture. until the 15th century. We use rudimentary means to protect ourselves from the wind and bad weather: Wooden shutters, waxed canvas, oiled skins or paper, all of which were best protected by wire netting. During the Middle Ages, there was a long period of stagnation in the use of window glass in houses, where the windows, which were shrinking in size, were barely glazed at all. At the beginning of the 14th century, the first glassworks were in Bézu-la-Forêt in the Eure department and Philippe Cacqueray was the inventor of flat sheets of glass. In 1698 at the Château de Saint-Gobain, Lucas de Nehou perfected the process of casting mirrors..
The manufacture of flat glass
Flat glass, or window glass, was made between the 5th and 10th centuries using two contemporary glass-blowing techniques:
- The glass-blowing technique known as “plateau”, “crown” or “cive” is also known as the “Normandy technique“. It is a technique produced in the west of France, where it reached its peak between 1700 and the middle of the 18th century. It was produced in England until the 19th century.
- The technique of blowing glass into a sleeve or board is also known as the “Bohemian” or “Lorraine” technique. It is produced in Eastern France and Central Europe.
These processes were used throughout the Middle Ages to make stained glass windows.
Blowing into a tray, crown or civet
It was not until the invention of this new process that flat glass really had a breakthrough.
The glassblower blows a bubble which he opens at one end. He then turns the bubble very quickly to obtain a flat disc. The cives can reach up to 80cm in diameter.
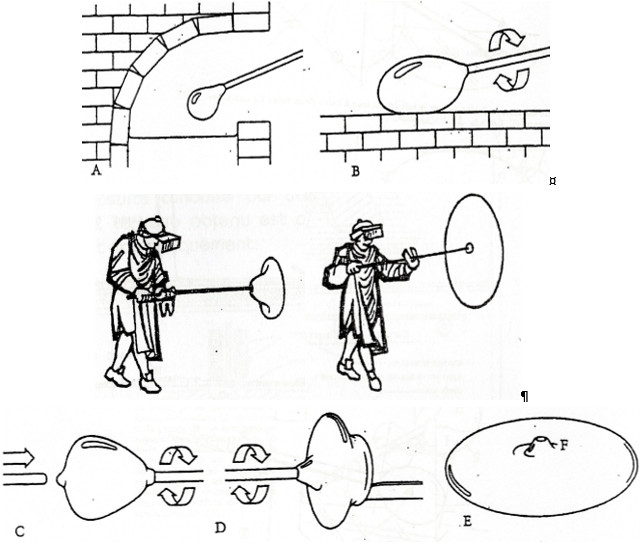
The first two operations (A&B) are the same in the 2 manufacturing modes.
In a rotating movement, the “paraison” ball is blown. (B). When the ball is large enough, attach another stick to the other end. Then remove the first stick used for blowing. (C).
The rotation is carried out until the civet is of sufficient size (D&E).
It is then detached from the “Pontil” and the centre of the civet forms a protrusion called a “Boudine” (F).
Video showing Catherine Farge making a contemporary Cive
Blowing into a sleeve or panel
A glass cylinder obtained by stretching the gob picked by the glassmaker, split, softened and flattened.
The glassmaker blows a bubble to form a hollow bottle, called a sleeve, and then cuts off the ends of the bottle. The resulting cylinder is cut lengthways and rolled out in an annealing furnace to produce a sheet of glass.
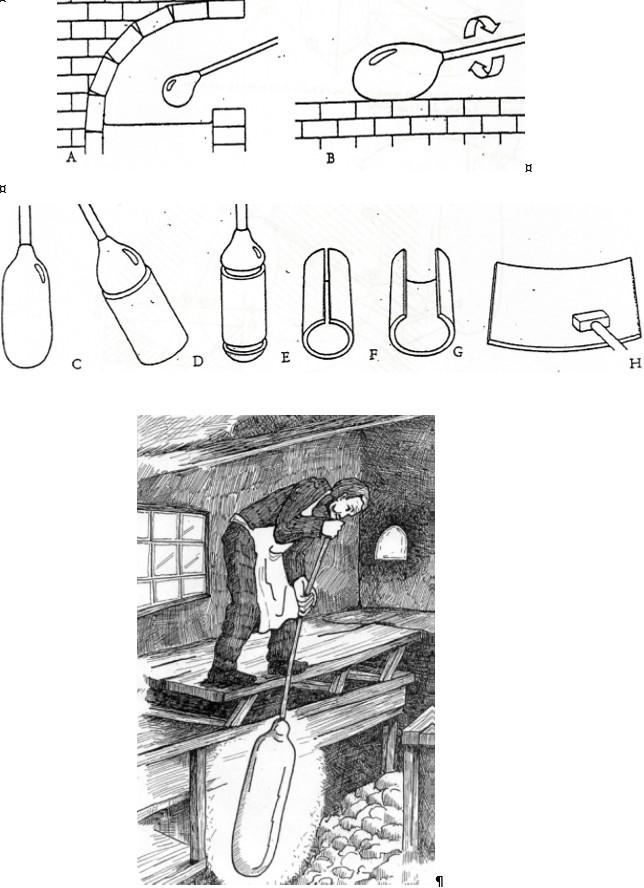
The glassmaker takes a ball of molten glass (A). He shapes it by turning it several times (B).
He blows it into a bottle shape (C&D), then cuts the cylinder at both ends.
The cylinder is called a “sleeve” (E ).
It splits the sleeve along its entire length (F&G). Then spread with a wooden spatula (H).
Video of contemporary sleeve production at Verrerie Saint Just
To find out more about how glass was made in the Middle Ages, visit the Musée de Cluny! c’est par ici !